
Comunity Lamp
Community Lamp was a project developed in the course of industrial design. The goal of the course was to understand the importance of industrial design in product development, with consideration to users, market, Product differentiation, and positioning.
The project revolved around producing a lamp for the first mars settlement. Furthermore, the product would be launched by the company Louis Poulsen complimenting their existing product line. On this page, I will describe the process of developing the Comunity Lamp, and give insight into our thoughts on the design and its production.


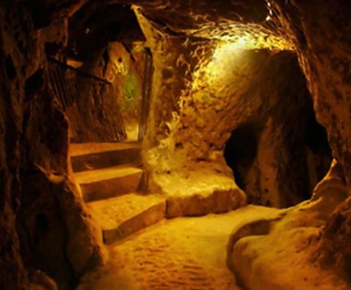

In regards to the environment for which the lamp is designed, we have designed the lamp as a streetlight hanging from the ceiling in a cave on Mars. NASA has found evidence that there are caverns on Mars. They theorize that these caves could be huge due to the relatively weak gravitation on Mars and could possibly contain future settlements. NASA further suggests that these caves would give protection against radiation, which would be crucial to a Mars settlement. We believe the caverns would be sealed airtight from the surface creating a biosphere, for self-sustainable breathable air.

Since the settlement on Mars will live underground, it will not be influenced by the cycle of natural sunlight, which is important for the community to synchronize their daily wake hours as well as the inhabitants' individual well-being. Therefore we believe that the streetlights on Mars will mimic the natural color and brightness of daylight on earth.

The lamp will be made from the fibrous network of fungi growing in a biomaterial also called mycelium. The biomaterial could conveniently be an organic waste. Mycelium gives the necessary strength and with its white matt surface, we believe it will spread the light from the lightbulb very nicely.
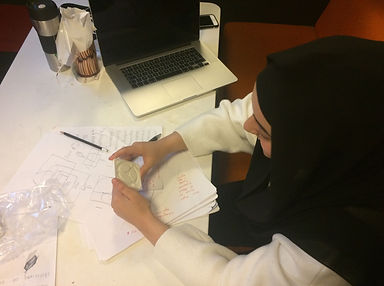

The process of producing the units to assemble the lamp is based upon cultivating the mycelium in growth molds. I have been responsible for planning the production, calculating the cost and energy consumption of the production. Planning manufacturing of a product is a skill which I have enhanced since then, in another course called manufacturing technology.
In the development of this project I designed and 3D printed the growth mold for presentation seen on the picture above.


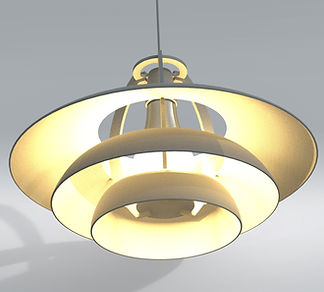.jpg)

In developing the lamp we made several models all of which I have been responsible for manufacturing. These are instrumental in order to better visualize the finished lamp. Each of the models have their own advantages and can be made as progressions into the final design.
The square cardboard is the fastest to build thus advantageous in the sense that it gives the quickest feedback on the size of the lamp.
The lamp in BlueFoam comes second in regards to building a model fast. However, this model gives a better sense of shape and form.
The CAD rendering showcases the aesthetics of the final product the best as lighting and different materials can be easily changed.
Lastly, we made a prototype, with 3D printed and laser-cut parts. We made it in tortilla which we also laser-cut as a means to get the prototype to look like it was made from mycelium.







The prototyping process has been quite iterative constantly refining the detail level of the lamp. Through my studies, I've spent a lot of time at the prototyping workshop at DTU building all kinds of projects, which have made me quite confident in using the different machinery as it can also be seen in my other projects.
Yep that actually happened!
Thank you for reading! I sincerely appreciate your interest in my creation piece. If you have any questions, comments or feedback regarding the creation, please reach out, I'll love to hear from you and give you my thoughts.
Consider subscribing to my newsletter at the footer of my website, that way you'll get notified by e-mail next time I'm posting a creation or a reading.